The new 4,800 square metre gypsum storage silo located in the Sydney Ports facility in Rozelle, has been constructed for Gypsum Resources Australia (GRA), a 50/50 joint venture between CSR and Boral. The facility will see 400,000 tonnes of gypsum pass through its doors over the next year.
"All of the gypsum entering the silo will come from GRA's gypsum mine at Lake MacDonnell, in South Australia," says Barry Loosmore, Project Manager on the GRA silo project. "The facility will accommodate 22 ships a year.
Lake MacDonnell, in South Australia is one of the biggest gypsum deposits in the southern hemisphere. The deposit is estimated at anything between 500 and 700 million tonnes, and about 1.2 million tonnes are shipped out a year. Gypsum is the principal constituent in plasterboards, such as Gyprock®. Gypsum stored at the GRA silo will be delivered to three main customers, CSR, Boral, and Lafarge, who will then process and manufacture it into plasterboard and related products.
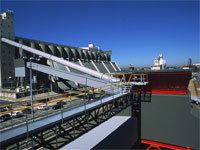
The new A$7.3 million facility includes three large wharf hoppers, into which the gypsum is unloaded from the ships. The gypsum is then transported on conveyors to a massive triangular A-frame store. The store has the capacity to contain 30,000 tonnes of gypsum at a time
Built to replace the previous, older bulk storage facility, the new store was designed by engineer, Phil Eiszele. "I was asked by CSR to come up with a concept for unloading their gypsum ships at Glebe Island in 1997," explains Phil Eiszele. "We came up with the design and obtained approval to build the facility, then the state Government decided to relocate it, so we had to start all over again. We obtained final approval in January 2003, and started construction thereafter."
Construction on the job went very quickly, it was completed in about ten months. However, there were several challenges to be overcome. "The major design constraint was the land area that Sydney Ports provided for us," says Phil Eiszele. "We were limited in a block which is only 32 metres wide and 150 metres long, and required to store up to 30,000 tonnes of product. We came up with the concept of the triangular structure because it minimizes the volume of the building - the gypsum stockpiles are basically big pyramids, so the building follows that shape."
A further constraint was Cement Australia's overhead pipeline, which ran right through the middle of the site. "The pipeline wasn't removed until the end of October, and we weren't able to continue building until it was gone," says Phil. "So we basically completed half the building in two months."
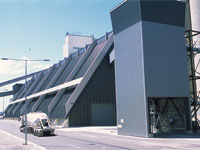
But its quick construction time isn't the only thing that makes this facility stand out from the crowd. Perhaps the most eye catching aspect of the structure is its unusual shape and design. The large A-frame store is clad entirely in COLORBOND® steel, with vertical fins of LYSAGHT CUSTOM ORB® in Windspray®. Running across the length of the building is a diagonal 'shadow break', a raised section of LYSAGHT CUSTOM ORB® in Dune®, which creates contrast and shadow on the building's flank
The conveyors and wharf hopper are also clad in a striking combination of LYSAGHT CUSTOM ORB® in Woodland Grey® and Windspray®, which contrasts effectively with the bright red of the hoppers' structural steel components.
"We chose LYSAGHT CUSTOM ORB® for durability and also for aesthetic reasons," says Phil Eiszele. "It was easy to use and gave us a good result. We also wanted to make sure that we used Australian products. We are an Australian company, and feel it's important to support local industry, and it was also cost effective to do so."
All the LYSAGHT CUSTOM ORB® on the project was supplied and installed by AB & M Constructions, a division of Butell Pty Ltd. According to Brett Butell, General Manager of Butell Pty Ltd, the need for the port to remain functioning throughout the project presented a challenge. "All of the conveyor sections were assembled on the ground, and then lifted up into place by cranes. The structural steel A-frames were all assembled on the ground and then stood up by crane as well. Everything was erected by mobile boom lifts, there has been no scaffolding whatsoever. We had to do it this way because the area is a working port and had to continue to function during the works."
"We used 6,000 square metres of LYSAGHT CUSTOM ORB® on the project," adds Brett. "The colours are fantastic, you combine the two soft greys with the red on the wharf hoppers, and it's pretty striking."
Brett says that Butell Pty Ltd has had a close relationship with BlueScope Lysaght for many years. "We are an established company, we've been around for 40 odd years. We've always worked with BlueScope Lysaght. They offer guarantees on all of their products, they have the backing of BlueScope Steel, and they are a really strong company."
"The delivery and lead times on LYSAGHT® products are also very reliable," Brett continues. "If you programme and plan properly, BlueScope Lysaght is always there to help you. It's been that way all the years that we've worked with them."
With the help of LYSAGHT® products, the project has been a complete success. So much so, that CSR intends nominating the facility for the Engineering Excellence awards this year. "Everyone's very happy with the result," says Phil Eiszele. "It's fantastic. It looks good and it works. It's a very unique structure and it's also probably the last large bulk store that will ever be built on Sydney Harbour, with the change in Government initiatives to minimize the ports. I don't think we'll see anything else this big built for a long time."