A Hunter Valley company whose modular conveyor gallery system has become an integral part of major Australian power generation, mining and minerals treatment facilities, has won its first major export order.
Redispan Conveyors Pty Ltd has developed its Modular Conveyor Gallery System from a product originally patented by the Down Engineering Group of Campbelltown, NSW.
In Redispan's hands the modular system has become world competitive for cost efficiency, environmental performance and versatility.
Workers at the company's Tomago plant have begun what Redispan describes as mass customisation of the design to supply nearly one kilometre of conveyor gallery for a minerals processing facility in Norway.
The company's systems are already in operation throughout Australia. One of the best known Redispan installations is the Port Waratah coal loader in Newcastle.
The Modular Conveyor Gallery System's distinctive profile is highlighted by roof cladding in LYSAGHT CUSTOM BLUE ORB® profile made from COLORBOND® Ultra steel.
Redispan's totally enclosed modular construction system was originally developed to ensure water containment during coal wash down, but soon won customers because of the additional benefits of noise, dust and spillage containment when handling a wide variety of materials.
The Redispan conveyor gallery roof sits atop a structural side cladding, a continuous structure to facilitate wash down and assist in load distribution, and a trestle system. A small footprint minimises site disturbance and the enclosed construction topped by a curved steel roof in LYSAGHT CUSTOM BLUE ORB® profile creates a tidy appearance.
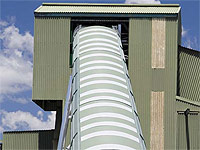
BlueScope Lysaght has supplied 5,000 square metres of its LYSAGHT CUSTOM BLUE ORB® profile steel to special order for the first Redispan export project. The CUSTOM BLUE ORB® profile material specified is rollformed in 0.80mm BMT (base metal thickness) double sided COLORBOND® Ultra steel in the non-standard colours Bronco Grey (underside) and Jello Green (top).
"We've used steel in LYSAGHT CUSTOM BLUE ORB® profile for every conveyor gallery system we have built," Redispan general manager, Peter Lee, said. "BlueScope Lysaght supply it curved and ready for installation.
"The profile is popular with customers and the choice of colours allows us to tailor appearances to suit the individual site, which can be important when you are dealing with a kilometre of roofing.
"Acoustic tests have also shown that the 0.80mm BMT thickness is very effective for the attenuation of noise at certain critical frequencies and the COLORBOND® Ultra grade steel from which the LYSAGHT CUSTOM BLUE ORB® profile is rollformed is suited to mine site and minerals processing environments.
LYSAGHT CUSTOM BLUE ORB® is the classic Australian corrugated profile. It has won an enduring place in local architecture for roofing and walling across the broadest range of applications including residential, industrial and commercial uses.
Peter Lee said that the curved roof design of the conveyor gallery was largely self cleaning and that the gauge used provided the ability to maximise weight savings on the supporting structure while still meeting noise attenuation targets.
Individual sections of the modular conveyor gallery system are assembled at Redispan's factory then shipped to site for erection. Single modules measure up to 18 metres, with widths between two and six metres. They can be joined to achieve spans up to 78 metres between support trestles.
Customised internal layouts can include one or two conveyors and single, double or triple walkways for maximum flexibility.
"Our modular gallery system is covered by multiple patents," Peter Lee said. "We are constantly investing in research and development to ensure it remains the system of choice for Australian resource projects as well as winning us export business.
"Factory fabrication enables us to maintain quality standards which just can't be achieved in the field with other systems."